At the most basic level, an edge is a V (bevel). Sharpness comes from making a perfect bevel, honing both sides to a mirror finish and honing the very tip to as sharp as possible. This article will explore what it is that makes a razor sharp, a brief explanation about steel, and how we hone a sharper razor. We will explore the different types of steels, their composition, and why heat treatment forms the backbone of any sharp instrument.
Article Outline
The Steel
Stainless Steel
Carbon Steel
Heat Treatment
The Edge
Establishing the Bevel
Polishing
A Sharper Razor
Verhoeven – Experiments on Knife Sharpening
The Steel
It all starts with the steel. In the beginning, there was bronze, obsidian, flint, and shells. Then came the invention of iron and with it, steel. Steel is the material of choice for tools and razors ever since it was invented all those years ago. Today there are many different types of steel, but the main two categories are stainless and carbon steel. The difference between the two is the introduction of chromium in stainless steel. This article will not go into martensite crystal formation or the technicalities about hardening steel.
Stainless Steel
Stainless steel is a misnomer, it should be called stain resistant steel. Stainless steel makes a good choice for straight razors because of its resistance to rust. Rust is the enemy of sharpness. The less your razor’s edge rusts, the sharper it remains and the less honing it requires. However, this has absolutely no effect on the initial sharpness of your razor.
Stainless steel can be a poor choice for straight razors. Stainless steel such as alloy 304, are a poor material with which to make a razor. Such alloys contain low levels of carbon and are ultimately unable to create and hold a sharp edge. Other stainless steel alloys perform more similarly to their carbon steel brethren and take a keen edge. These alloys have the added benefit of toughness and corrosion resistance. Other alloys only add a small amount of chromium sacrificing rust resistance and toughness for a sharper edge.
As a general rule, stainless steel does not take as good an edge as carbon steel, but has better toughness and corrosion resistance. The toughness consequently makes stainless steel razors much harder to hone.
Carbon Steel
Carbon steel is the oldest steel known to man. Without the addition of chromium, carbon steel rusts easier than stainless steel and requires more care. The general rule is that the greater the carbon content, the sharper the edge you will be able to achieve; up to a certain point (it also makes the steel more brittle). There are too many alloys of carbon steel to count. Silver steel and tool steel are two of the most commonly known names. Silver steel is discussed in our history of the straight razor. It is called silver steel because of the high carbon content. Tool steel is similar to silver steel in that it also has a high carbon content, but it is more modern.
As a general rule, carbon steel razors take a keener edge initially, but will go dull faster. Consequently carbon steel razors are easier to hone. It should also be noted that because of the huge amount of variation, carbon steel razors will take and hold edges much differently from each other, especially across manufacturers, model lines, and time periods.
Heat Treatment
This is the most important part of the razor manufacturing process. The heat treatment turns soft steel into hardened steel. Soft steel is unable to hold an edge. It must be heat treated in order to create the martensite formations which enable edge formation and retention. Briefly explained, the steel is heated to a very high temperature, and then cooled quickly. Heat treatment is often confused with temper or tempering. Tempering is the process of taking the hardened, but brittle steel and taking some of the brittleness out at the expense of hardness. Tempering is basically just baking the razor for a set period of time in order to give spring back to the steel.
The Edge
A razor’s edge looks like a V in the cross section. Close-up electron microscope photos show that the edge does not end in a perfect V, but it comes pretty darn close. Consequently, to sharpen a razor, the sharpener must establish a perfect bevel. Establishing the bevel is the most important part of sharpening/honing, whether it be knives or razors, the basic principle is the same. Sharpen the two sides until they form a V. Once the bevel is established, the edge must be polished and the jaggedness reduced or removed. This is what separates a razor from a knife.
The polishing process begins at the 4,000 grit level. A skilled straight razor shaver can shave with a razor honed with just a 1,200 grit stone, but take it from me, it is barely acceptable and your face will feel pretty raw. A razor honed on a 4,000 grit stone feels much better, but 8,000 is universally held to be “shave ready.” We don’t call a razor finished until a much finer grit is reached.
Establishing the Bevel
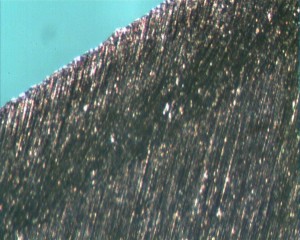
Establishing the bevel is the first part of any sharpening procedure. As stated earlier, a proper bevel should form a V. An improper bevel will instead form something similar to U or \_/. As you can see, the actual cutting edge does not form an edge. The two sides of the bevel do not meet in the center. The solution is more honing until the edges meet.
The purpose of establishing the bevel is to bring the two sides of the bevel into the center. To hone the two sides until they form a proper edge. If the edge is not formed, the razor will not cut. Without an edge, no matter how much you polish the two sides of the bevel, the razor will never shave. To make the two sides meet in the middle, the sharpener must hone away the steel until \_/ turns into \/. After the edge is formed and the razor becomes a sharp knife, the goal is to further refine the edge, turning \/ into V. The next step is known as polishing.
Polishing
Once the bevel is established, the edge must be polished. Even though the razor is sharper than a really sharp knife, the edge is not smooth, it is jagged and does not form a perfect V yet. The edge can be refined further, the jaggedness can be removed and the edge’s width can be further reduced. This process is known as polishing and involves finer and finer stones.
While a 4,000 grit edge is shave-able, most men do not find such an edge to be satisfactory. Thus, 4,000 is only the first stepping stone on the road towards shave ready. Progressing through 8,000 and 12,000, the razor’s edge is refined and given a near mirror finish. The fine grit of these stones reduces the width of the actual edge by taking fewer and fewer steel particles off the edge. The polishing process works because the steel will reflect the characteristics of the stones it is being honed on.
A Sharper Razor
It is universally accepted that 8,000 is shave ready. Most people stop at 12,000 or thereabouts and call it truly shave ready and comfortable. Some people and hone-meisters will go a step further and use diamond sprays or chromium oxide (~.25-.5 µm). These pastes do not give the same edge as a stone, but they do produce a very polished bevel. The edge given off these pastes is harsh. Probably due to the nature of the substrate the paste is put on. A Sharper Razor uses the equivalent of a 50,000 grit stone to finish your razor. Our finishing stones have been lapped perfectly flat and give you a superior edge. We put a mirror finish on your razor’s edge and go beyond shave ready.
It is our mission to continually search for the means to hone a sharper razor.